Optimierung des LPBF-Prozesses zur Fertigung von Brennkammersegmenten aus Haynes 282
Der Laser Powder Bed Fusion (LPBF)-Prozess ermöglicht die Fertigung von Bauteilen mit komplexen Geometrien und feinen inneren Strukturen, die mit traditionellen Fertigungsmethoden nur schwer oder gar nicht realisierbar sind.
Merken
Der Laser Powder Bed Fusion (LPBF)-Prozess ermöglicht die Fertigung von Bauteilen mit komplexen Geometrien und feinen inneren Strukturen, die mit traditionellen Fertigungsmethoden nur schwer oder gar nicht realisierbar sind. Ein bemerkenswertes Beispiel für den Einsatz dieser Technologie ist die Herstellung von Brennkammersegmenten mit integrierten Schindeln des Typs P10X bei Rolls-Royce. Dieses innovative Design verbessert die Verbrennungseffizienz und reduziert NOX- und Partikelemissionen, indem es die Vormischung von Kraftstoff und Luft optimiert. Die Herstellung der Brennkammer als geschlossener Ring stellt jedoch eine Herausforderung dar, da das Drucken steil geneigter Wände ohne Stützstrukturen nur durch präzise Prozessoptimierung erfolgreich umgesetzt werden kann.
In Zusammenarbeit mit Rolls-Royce Deutschland hat die CHESCO GmbH eine Parameterstudie unter Verwendung des „High Energy Down Skin“ (HEDS)-Ansatzes durchgeführt, um Brennkammersegmente aus Haynes 282 erfolgreich ohne Stützstrukturen zu fertigen. Ziel war es, den Wärmeeintrag beim Drucken des Downskin-Bereichs durch gezielte Parameteranpassungen zu erhöhen, um eine ausreichende Haftung des geschmolzenen Pulvers im Pulverbett sicherzustellen und somit einen stabilen Druckprozess zu ermöglichen. Die Studie ergab einen optimierten Parametersatz, der die gewünschten Materialeigenschaften erreichte: eine Porosität unter 0,1 %, eine Oberflächenrauheit des Downskin-Bereichs von etwa 50 μm sowie die angestrebten Formtoleranzen der integrierten Kühlkanäle von 0,3 mm.
Vortragssprache: DEU
Referent*innen (1)
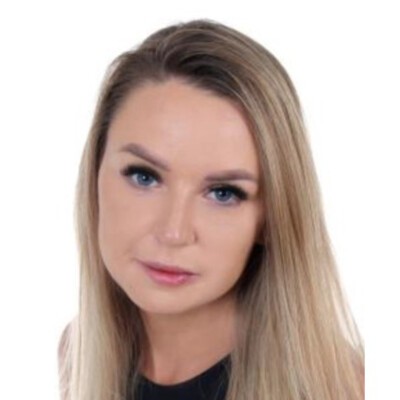