Combination of 3D-printing and investment casting processes in the development of components for aerospace applications
TITAL GmbH has been producing high-quality aluminum and titanium castings for the aerospace industry using the investment casting process since 1974. The process presented enables the highest dimensional accuracy, optimal material utilization and complex geometries.
Bookmark
Since 1974 TITAL GmbH manufactures high quality castings from aluminum and titanium alloys solely according to the lost wax process, mainly for the aerospace industry.
The advantage of this process, besides its high dimensional accuracy and excellent material consistency, is the optimised use of material as this process enables the implementation of complex geometries such as undercuts etc.
Because of this, topologically optimised designs can be realised with nearly no limitations.
This is possible because of the use of lost patterns and lost molds. For prototypes and small production batches such patterns are built using the SLA- or PMMA-process.
The combination of topology optimization, generative manufactured RP-models and the investment casting process enables the designer to realize operational prototypes at maximum flexibility without loss of quality.
Further advantages of this combination are the feasible part sizes, as well as the unrestricted usability of such parts because of the well-established and approved processes.
Presentation language: GER
Speakers (1)
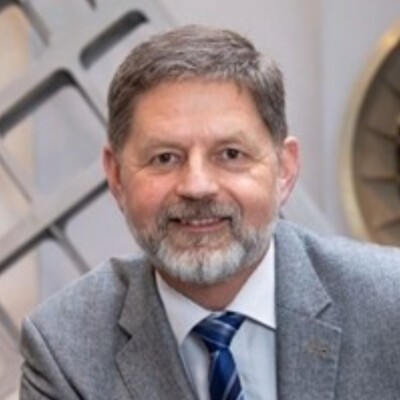