Optimization of the LPBF process for the production of combustion chamber segments from Haynes 282
The Laser Powder Bed Fusion (LPBF) process enables the production of components with complex geometries and fine internal structures that are difficult or even impossible to achieve with traditional manufacturing methods.
The Laser Powder Bed Fusion (LPBF) process enables the production of components with complex geometries and fine internal structures that are difficult or even impossible to achieve with traditional manufacturing methods. A notable example of the application of this technology is the production of combustion chamber segments with integrated P10X-type blades at Rolls-Royce. This innovative design improves combustion efficiency and reduces NOX and particulate emissions by optimizing the premixing of fuel and air. However, manufacturing the combustion chamber as a closed ring presents a challenge, as printing steeply inclined walls without support structures can only be successfully achieved through precise process optimization.
In collaboration with Rolls-Royce Germany, CHESCO GmbH conducted a parameter study using the "High Energy Down Skin" (HEDS) approach to successfully manufacture combustion chamber segments from Haynes 282 without support structures. The goal was to increase the heat input when printing the downskin area through targeted parameter adjustments, ensuring sufficient adhesion of the molten powder in the powder bed and thus enabling a stable printing process. The study resulted in an optimized parameter set that achieved the desired material properties: a porosity of less than 0.1%, a surface roughness of around 50 μm in the downskin area, and the targeted form tolerances of the integrated cooling channels of 0.3 mm.
Presentation language: GER
Speakers (1)
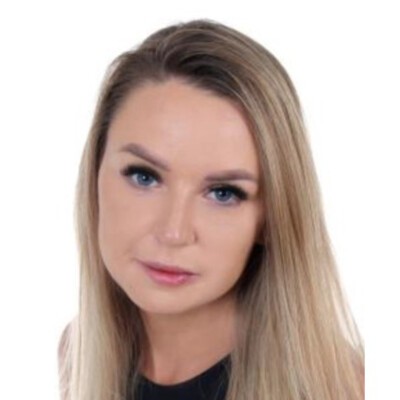