Micro-SLM and Macro-SLM – powder bed-based additive manufacturing in new dimensions
Get to know the process principles of micro-SLM and macro-SLM, its advantages and special features as well as application examples.
Bookmark
Laser-based additive manufacturing of metal components is a central research focus at the Laserinstitut Hochschule Mittweida (LHM). Two processes in particular represent special development highlights here: Micro-SLM and Macro-SLM. Both technologies are further developments of the established selective laser beam melting (also known as SLM or L-PBF), which open up new dimensions beyond the limits of this process. Micro-SLM enables the production of high-precision components with structural resolutions of up to 30 μm and layer thicknesses of just 5 μm. Compared to the conventional SLM process, this means an improvement in resolution by a factor of 4 to 5, which opens up completely new fields of application. The already very low surface roughness of only Ra = 2.5 μm directly after printing can be reduced to up to 0.1 μm by post-processing. Current product examples include highly efficient micro heat exchangers and topology-optimized mirror holders for precise alignment of inter-satellite laser communication. The Macro-SLM addresses the opposite size range and is used to produce large-volume components with high build rates. The structure resolutions here are in the millimeter range instead of the micrometer range, which enables a very high build rate of up to 10 kg/h. The first large components have already been produced quickly and cost-effectively on the current research system with a build volume of 2 × 2 × 1 m³, which impressively demonstrates the advantages of this technology.
Presentation language: GER
Speakers (1)
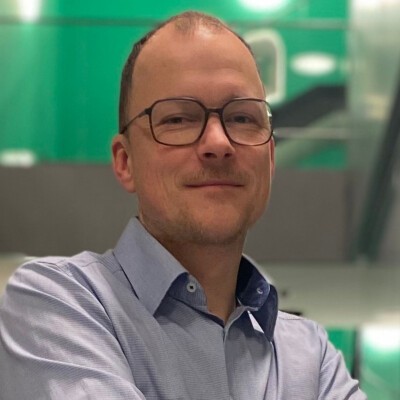