Innovative additive multi-material gripper solutions for injection molding automation
Functional integration in the component, weight reduction and individuality through additive manufacturing
Gripper for injection molding automation. The removal module was designed for packaging applications. In this special customer application, flower pots (4 compartments) are removed in a total cycle time of 3.2 seconds. This is done with the help of an integrated membrane, which is filled with air. This “tensions” the part so that the air is released when it is placed on a conveyor belt. The removal module is additively manufactured as a two-component part. The base ring is made of PC/ABS and a soft membrane is made of TPU. With the freeformer process, up to three different materials can be used in one component.
Advantages: Thanks to the innovation of additively manufacturing the gripper using two components in one print, the entire gripper could be made lighter. This weight saving means that a more compact and therefore more cost-effective handling system can be used to remove the products. However, the gripper itself is also significantly cheaper than a conventionally manufactured one, as the actual removal and blow-off function has been integrated directly into the component. This functional integration means that no additional external, mechanical grippers are required. The manufacturing costs of the removal module could therefore be reduced by a factor of 2. Thanks to additive manufacturing, functions can be integrated directly into grippers and manufactured more quickly and individually. Used grippers can also be replaced quickly and cheaply. This is only possible using 3D printing. The partner company here is OSKO.
Presentation language: GER
Speakers (1)
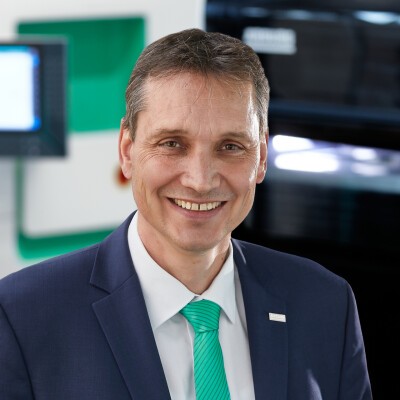