Faster manufacturing design of custom-made orthotics and prosthetics using Bluetooth 3D scanning textiles
Discover an innovative solution to replace the use of plaster cast in the design of orthotics and prosthetics
The first stage in the process of designing custom-made orthoses and prostheses for patients is still currently based on plaster casts. Although the rest of the manufacturing process can use digital tools to make the best and most efficient design possible, the crucial step of measuring the patient, assessing the tissue and correcting the posture can still only be done with plaster. A faster, cleaner, more accurate method that can be directly integrated into manufacturing processes is proposed in this presentation.
The study concerns ankle-foot orthoses (AFOs). Five Bluetooth 3D scanning textiles to be placed on the patient at anatomical points of interest provide, in a matter of seconds, a 3D file representing the patient's lower limb required to make an AFO. Thanks to 528 magnetic sensors placed in these textiles and low-field magnetic tracking, it is possible to obtain a point cloud which is then interpolated by statistical shape model algorithms. Measurement performance was evaluated at a signed Euclidean distance of 0.64 mm ± 2.6 mm, below the error of plaster casts which is of the order of 5 mm. An exportable STL file enables the AFO to be made easily with any CAD software.
Presentation language: EN
Speakers (1)
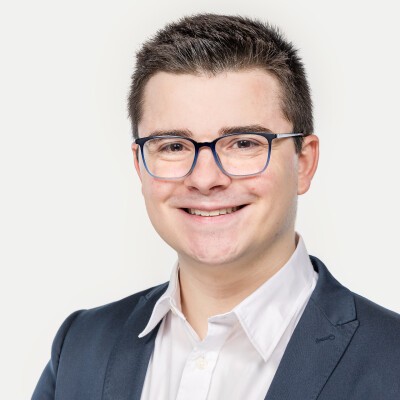