Laser-based powder bed fusion of WC-Ni for additive manufacturing of wear resistant tool components
The study demonstrates how WC-Ni composites can be processed using PBF-LB/M and sintering HIP. This process enables dense, wear-resistant components with high strength and complex designs.
Laser-based powder bed fusion (PBF-LB/M) enables the additive manufacturing of complex geometries in hardmetals such as tungsten carbide-cobalt (WC-Co), which are widely used in cutting tools due to their hardness and thermal resistance. However, the process faces challenges including binder evaporation, the formation of brittle phases, and unwanted grain growth.
In this presentation, the use of WC-Ni as an alternative material system for PBF-LB/M is explored. Two processing routes were investigated: a conventional single-stage PBF-LB/M process and a two-stage approach combining low-energy PBF-LB/M with subsequent hot isostatic pressing (HIP). The two-stage route enabled the production of dense WC-Ni parts with refined microstructures and improved mechanical performance compared to WC-Co processed under similar conditions.
Based on the developed process, tool demonstrators were successfully produced and tested in real machining conditions. The results indicate that WC-Ni with controlled PBF-LB/M and sinter-HIP processing offers a promising alternative to high-strength and high-hardness steels for abrasion-exposed components, combining hardness and toughness with design flexibility.
Presentation language: EN
Speakers (1)
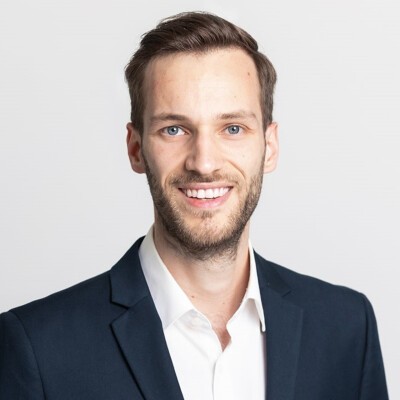
Leon Engelhardt
Research Assistant, Transfer Center for Intelligent Production Systems Rheinische Hochschule Köln